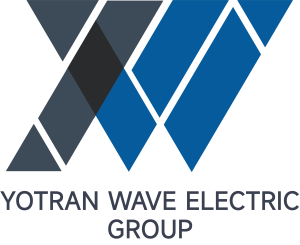
Yotran Wave Electric's SZ-13000/115 is a high-efficiency 13MVA power transformer designed for 115 kV/xx kV voltage conversion, compliant with IEC, IEEE, and GB standards. Key features include:
Ideal for substations, industrial plants, and renewable energy integration, this transformer offers a 40+ year design life with customizable options (taps, bushings, protection systems). Robust construction and advanced insulation ensure reliability in demanding environments.
The SZ-13000-115/10.5 is a high-efficiency electrical transformer designed for step-up/step-down applications, featuring an ultra-low-loss silicon steel core. With no-load loss ≤15kW and load loss ≤70kW (GB/T 6451 standard), it achieves >99.2% efficiency, reducing operational costs by 10-15% compared to conventional models. Ideal for utilities and industrial plants seeking energy-saving power transformer suppliers.
Equipped with ONAN/ONAF cooling, this power transformer ensures stable operation in harsh environments (-30°C to +45°C). Its smart temperature control enables 120% overload capacity for 2 hours, making it perfect for renewable energy integration. Customers looking to buy power transformer online benefit from its reliable performance.
Fully compliant with IEC 60076, IEEE C57.12, and GB 1094, this transformer holds UL/cUL, KEMA, and CE certifications. Its 8% short-circuit impedance and reinforced structure pass rigorous testing, ensuring a <0.3% annual failure rate. Trusted by global ODM/OEM transformer partners.
Tailored solutions include ±8×1.25%/±9×1.78% on-load tap changers, <65dB noise reduction, and C5-M anti-corrosion coating. With 200+ successful global deployments, we offer a 12-week lead time—contact us for a transformer price list or project-specific requirements.
Type | Step down power transformer |
---|---|
Model | SZ-13000-115±9*1.78%/10.5 |
Cooling Method | ONAN/ONAF |
Primary Voltage | 115kV |
Secondary Voltage | 10.5kV |
Rated Frequency | 50HZ |
Rated Power | 13MVA |
Winding Material | Copper |
Voltage Regulation | OLTC |
Tapping Range | ±8×1.78% |
Connection Group | YNd11 |
Transformer Dimension | 6200×4200×5000mm |
Weight | 33000kg |
Application Scenarios of Power Transformer:
Below are generic installation and use instructions for 110kV class power transformers: